Manufacturing Execution Systems
MES Philosophy
The MES landscape can be complex and intimidating, as the acronym is broadly applied to any functionality that falls between the Enterprise Resource Planning systems and the plant-floor Automation systems. As a result, Verus looks beyond software functionality and approaches each MES engagement with the goal of improving two fundamental areas: Human Engagement, and Process Governance.
Human Engagement - How can we improve the tools available to decision makers, influence operations in real time, and optimize workflows to streamline the manufacturing process?
Governance - How can the system reinforceoptimal business processes through embedded standard practices, processparameter management, and quality controls?
Guided by these principles, the team selects the appropriatesoftware, methods, and practices to ensure business value is realized in every MESproject.
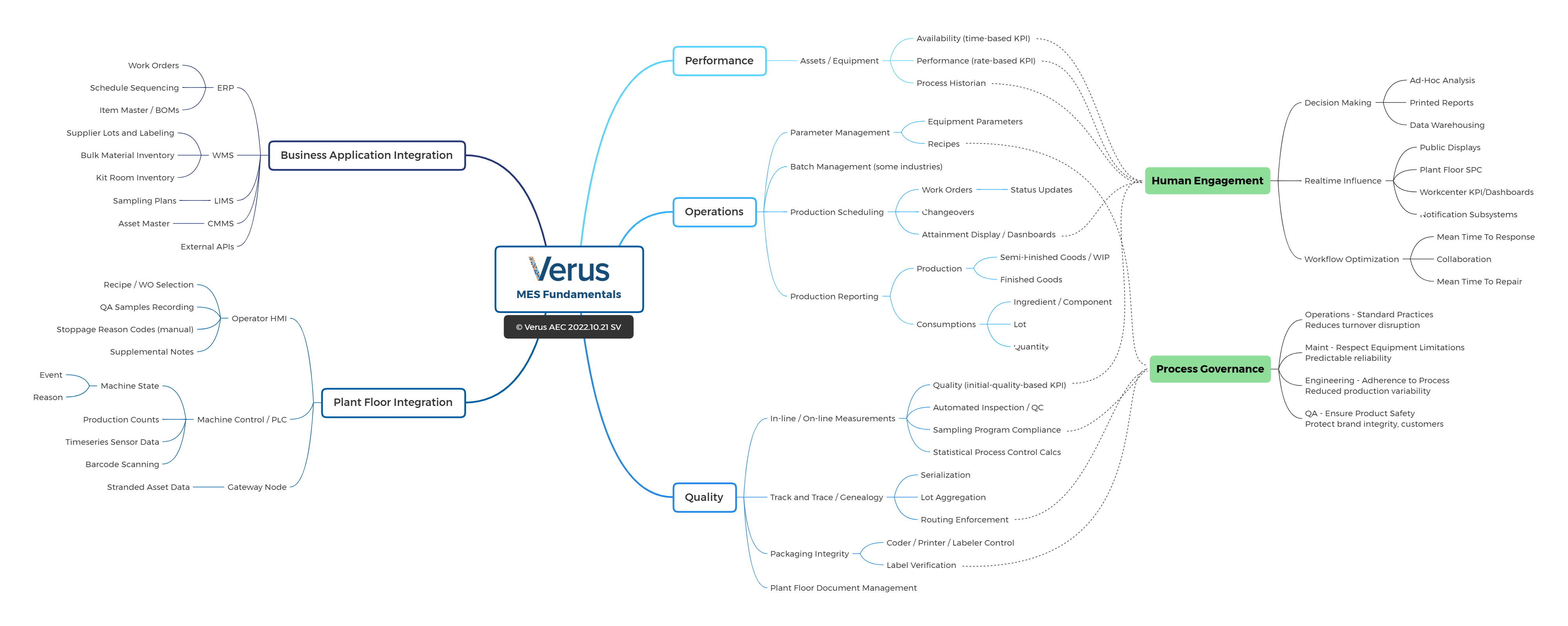
Scope of MES
One or more of the following aspects of an MES implementation come together to aid manufacturers with continuous process improvement.
1. Operations: Model the facility processes to enable the system to identify individual jobs or work cells of the production lines. ERP systems include high-level operations, and then the MES system maps those ERP operations into smaller chunks to allow for more granular real-time tracking on the plant floor. The operations model along with the bill of materials (BOM) helps enforce that operators use the correct parts or ingredients for the given process order.
2. Performance: Utilizing the operations model, machine I/O, and human input, the system delivers overall equipment effectiveness (OEE) by combining the factors of machine availability, downtime, and performance. Reason codes selected for downtime events can provide pareto charts to determine the most likely causes for failures and production bottlenecks. The data may also be used to measure the mean time to repair (MTTR), and mean time between failures (MTBF).
3. Quality: Allows manufacturers to specify targets and upper/lower bounds to measurable aspects of their product to determine when to scrap or rework certain parts or batches. Data collected can aid in statistical process control (SPC) to identify issues with the machinery or control system, and ensures the finished product is as close to specification as possible. The MES quality system can either serve as the laboratory information management system (LIMS) or interface with an existing LIMS to gather information resulting from testing performed away from the production line.
4. Track and Trace with Genealogy: The system records exactly which material lots or parts were used in the semi-finished and finished goods through each operation in the model. In this fashion, the system can output a complete genealogy of the product after any step in the process. This allows manufacturers to accurately recall their products based on any of the input material lots turning up defective. For some manufacturers, this functionality can aid in determining when a part or batch is ready for next steps.
5. Production Scheduling: MES can assist with plant floor production schedules – especially when there are multiple lines that make the same product. The ERP system may define what needs to be done and when, and MES allows plant personnel to assign the work to the lines in a logical fashion to achieve the production goals.